Welding WPS Explained: Key Components and Benefits for Your Welding Processes
Welding WPS Explained: Key Components and Benefits for Your Welding Processes
Blog Article
Grasping Welding WPS Standards: Ideal Practices and Techniques for Quality Welds
In the world of welding, grasping Welding Treatment Requirements (WPS) criteria is a crucial element that directly affects the high quality and stability of welds. As we browse through the intricacies of welding WPS requirements, uncovering vital insights and strategies for attaining top-tier welds will be paramount for welders seeking to excel in their craft and generate welds that stand the examination of time.
Recognizing Welding WPS Criteria

Assessors rely on WPS documents to verify that welding treatments are being adhered to properly and that the resulting welds are of high top quality. Designers utilize WPS requirements to make welding procedures that make sure the resilience and reliability of bonded frameworks.
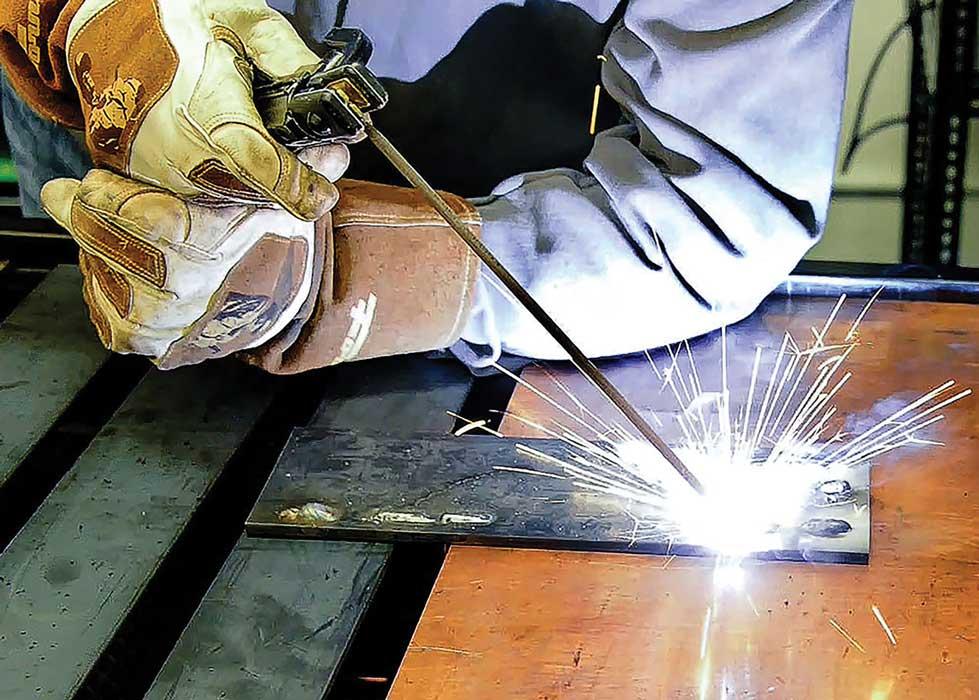

Important Devices for Top Quality Welds
Mastering welding WPS requirements is essential for welders to successfully make use of the vital devices needed for producing top quality welds. The type of welding maker needed depends on the welding process being used, such as MIG, TIG, or stick welding. Cable brushes and damaging hammers are important for cleansing the weld joint before and after welding to get rid of any pollutants that could affect the high quality of the weld.
Trick Methods for Welding Success
To accomplish welding success, one must grasp the key methods necessary for generating top quality welds. One vital technique is keeping the right arc size. Maintaining the electrode at the optimal distance from the workpiece is vital for developing strong, uniform welds. In addition, managing the traveling speed is critical. Moving as well promptly can lead to inadequate penetration, while moving as well slowly can result in too much warmth input and prospective defects. Proper adjustment of the electrode angle is an additional vital method. The angle at which the electrode is held can influence the bead form and penetration of the weld. Additionally, making sure constant weapon angle and instructions of traveling is important for uniformity in visit here the weld bead. Finally, maintaining a secure welding and a constant hand placement throughout the process is crucial to attaining accuracy and consistency in the welds. By mastering these key methods, welders can boost the quality of their work and accomplish welding success.
Ensuring Conformity With WPS Standards

Furthermore, keeping comprehensive records of welding parameters, equipment calibration, and examination results is important for demonstrating compliance with WPS criteria. By vigilantly sticking to WPS standards, welders can ensure that their job satisfies the required quality degrees and contributes to the total success of the welding job.
Troubleshooting Common Welding Issues
To resolve this, ensuring proper cleaning of the base steel prior to welding and utilizing the proper securing gas can dramatically lower porosity. Furthermore, distortion, splitting, and spatter are common welding challenges that can be alleviated with proper joint preparation, regular heat control, and choosing the suitable welding consumables. By extensively understanding these common welding problems and their origin triggers, welders can efficiently troubleshoot problems and accomplish high-quality welds.
Final Thought
In final thought, mastering welding WPS standards needs a comprehensive understanding of the standards, using Read Full Article important tools, and implementing essential techniques for effective welds. Guaranteeing conformity with WPS requirements is essential for creating quality welds and avoiding common welding concerns. By adhering to finest techniques and practices, welders can attain consistent and trusted results in their welding tasks.
In the world of welding, grasping Welding Treatment Specification (WPS) criteria is a critical part that directly affects the high quality and integrity of welds.When diving right into the realm of welding techniques, you could try these out a vital facet to comprehend is the significance and details of Welding Procedure Requirements (WPS) standards. WPS criteria provide a comprehensive guideline for welding procedures, making sure consistency, top quality, and safety in the welding procedure. The type of welding maker needed depends on the welding process being used, such as MIG, TIG, or stick welding.Achieving welding success with the mastery of essential methods necessitates a detailed understanding and adherence to Welding Procedure Specification (WPS) criteria.
Report this page